Business Models for CO2 Mineralisation
15.03.2022
The cement industry is responsible for about seven per cent of global greenhouse gas emissions. To encourage the decarbonisation of this industry, policymakers and the industry must find ways to incentivise reductions. A study from the Heriot-Watt University and the Institute for Advanced Sustainability Studies (IASS) gives us a first look at how CO2 mineralisation can reduce emissions from cement production by up to 33 per cent at no additional cost – under the right conditions.
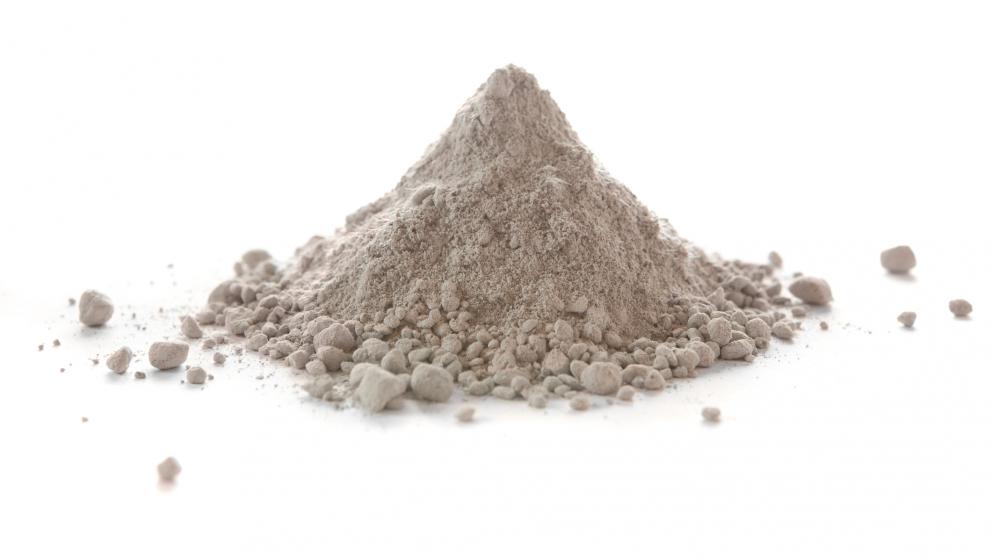
Cement’s global market size is projected to reach $463 billion by 2026 – around six gigatons of cement per year – so reducing the industry’s emissions is crucial for climate mitigation. About 60 per cent of emissions from the cement industry are process-inherent because they result from the calcination of limestone. In calcination, high temperatures are used to remove carbon dioxide from limestone. The product is called clinker. Emissions from this process are very difficult to reduce because to do so, the entire process would have to be replaced by low-emission alternatives, or the emitted CO2 would have to be captured and stored permanently.
While replacing cement and concrete with alternative building materials like wood would require an unrealistically rapid change of the entire construction value chain, carbon capture and storage technologies provide an alternative – but they incur additional production costs. So the cement industry needs to find ways to mitigate CO2 emissions that generate additional revenue, not higher costs. This is where CO2 mineralisation comes in. In CO2 mineralisation, the captured CO2 reacts with minerals (e.g., magnesium-rich or calcium-rich silicates) and can be stored permanently – and the resulting product could even bring in additional revenue.
Trade certificate eligibility and government support essential
The authors of the study, recently published in Communications Earth & Environment (Nature Portfolio), show that under certain circumstances, the use of mineralisation products can lead to positive business cases. The researchers further developed existing mineralisation processes to produce cement additives in different compositions that can be added to ordinary cement. Using an integrated techno-economic model, they were able to identify the conditions that lead to positive business scenarios. They also uncovered the most important factors for the improvement and large-scale implementation of these technologies by means of a global uncertainty analysis.
Their conclusion: Integrating CO2 mineralisation into the cement production process can reduce CO2 emissions by eight to 33 per cent. According to first author Till Strunge, this can bring an additional profit of up to 32 euros per tonne of cement, provided certain conditions are met: “The products need to be used as cement substitutes in cement mixtures in construction, for example, in bridges or buildings, and cement standards may need to be adjusted. Moreover, CO2 storage in minerals must be eligible for ETS credits or similar.” He also stressed the importance of mineral transport and product composition.
Strunge believes that ETS and even CO2 taxes alone will not be sufficient to establish more low-carbon solutions in the cement industry on the market. For this reason, he and his co-authors recommend mechanisms such as subsidy programmes like those once used for wind and solar power. “Governments should also invest in first-mover low-carbon cement plants.”
Publication:
Till Strunge, Phil Renforth and Mijndert Van der Spek: Towards a business case for CO2 mineralisation in the cement industry, Communications Earth & Environment 03/2022. DOI: https://doi.org/10.1038/s43247-022-00390-0